Linde Warehouse Navigator: A modular warehouse management system with forklift navigation
The Linde Warehouse Navigator helps small and medium-sized companies to digitally organize their entire warehouse processes. Consisting of a warehouse management system as well as an order picking and forklift guidance system, the modular solution enables long-term time and cost savings to be achieved and features various special options: A three-dimensional view visualizes the warehouse including goods in real time and shows drivers the fastest route to their destination. While doing so, the software automatically documents the movements of the load carriers across different storage locations.
Many small and medium-sized companies in Germany and other European countries still handle their warehouse processes manually using tables, lists and paper printouts. “In the long run, however, this is neither efficient nor up-to-date and is detrimental to profit and competitiveness,” says Christoph Hock, Product Manager Software Solutions. “Even with fleets of three or four forklifts, it quickly becomes confusing when incoming and outgoing goods processes as well as storage and retrieval operations are organized using paperwork.”
The Linde Warehouse Navigator provides a solution in the form of digital warehouse management. Its range of functions can be adapted to different warehouse scenarios and expanded step by step. The developers placed great importance on providing clear, configurable user interfaces, and ensured that mobile devices can be integrated in the system. Training and go-live support are part of every package solution. The required software licenses can be either purchased or rented via a monthly fee. This also includes the charges for cloud hosting.
Reliable goods tracking and complete overview
Once installed, the Linde Warehouse Navigator can be used for the paperless control, monitoring and documentation of all orders and inventories as well as goods movements in the warehouse. The basis is the warehouse management system (WMS) which is suited for all warehouse types as well as standard storage and retrieval strategies. “In addition, even the entry-level version offers customers an overview of specific key figures on the basis of which they can further improve their processes,” says Christoph Hock.
For Product Manager Hock, the highlight of the software is that it enables 3D visualization of all storage locations that shows the current occupancy for the entire plant site. Selected items are color-coded so that their position in the warehouse is easy to identify. “This function is particularly helpful for block warehouses,” says Hock. In addition to this is the continuous tracking of load carriers via the optional Real-Time Locating System (RTLS).
In conjunction with the RTLS, the forklift guiding system (FGS) coordinates the routes of the industrial trucks in real time and displays all forklifts and AGVs operating in the warehouse. Transport orders are either generated manually by the employees, for example via the “drag-and-drop” feature in the warehouse visualization system or via a forklift call system (call button). Alternatively, orders can also be assigned automatically, for example from the ERP system via an interface or when predefined thresholds are not met. The optimal route to the destination is shown to the drivers via arrows in the 3D view. The source and destination of the transport order are also highlighted in color.
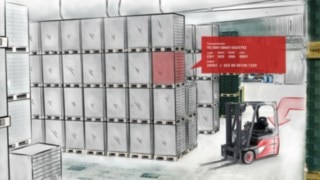
A special option of the Linde Warehouse Navigator is a three-dimensional view of the warehouse. Selected items are color-coded and in addition, the software shows drivers the fastest route to their destination.
The third component of the Linde Warehouse Navigator is the order picking system. The system bundles smaller orders with various individual items for parallel picking (multi-order picking). Larger orders can be divided into several partial orders and consolidated afterwards.
Last but not least, the software solution helps harmonize the operational IT landscape and reduces the number of contacts involved. Very narrow aisle trucks and AGVs can be integrated via standard interfaces. “This ensures short commissioning times and reduces costs,” explains Christoph Hock.