The Complete Guide to Choosing Between Sit-Down and Stand-Up Forklifts
Key Takeaways
Introduction
Did you know that choosing the wrong forklift for your operation can reduce warehouse productivity by up to 30%? I’ve seen it happen more times than I can count during my years managing warehouse operations.
The decision between sit-down and stand-up forklifts isn’t just about operator preference—it impacts your bottom line, safety records, and overall operational efficiency. As someone who’s made both good and bad choices in this department, I can tell you that understanding the key differences is essential.
In this guide, I’ll walk you through everything you need to know about sit-down and stand-up forklifts. You’ll learn their basic characteristics, safety considerations, ergonomic factors, and cost implications. By the end, you’ll be equipped to make the right choice for your specific needs.
Let’s get into the nitty-gritty details that most sales reps won’t tell you about!
What Are Sit-Down Forklifts?
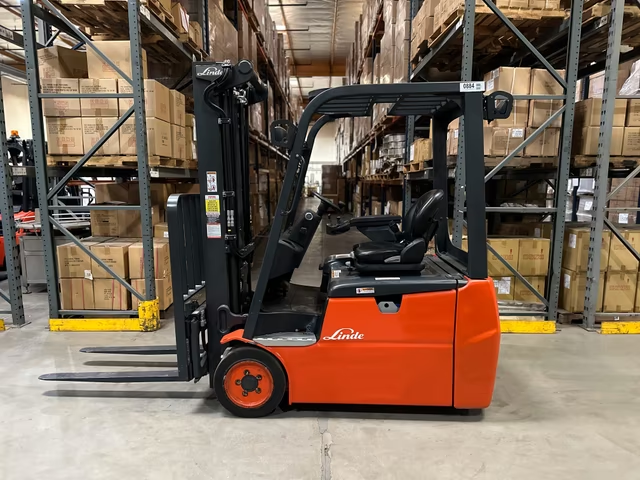
The Linde 346 electric 3W sit down forklift
Sit-down forklifts are exactly what they sound like—lift trucks where the operator sits during operation. They’re the most common type you’ll see in warehouses and distribution centers across the country. I remember when I first started in warehouse management, these were pretty much the only option we considered.
The biggest identifying feature of sit-down forklifts is their counterbalanced design. They use a heavy weight at the rear to offset the load carried on the forks. This counterweight might be metal (in IC models) or a combination of metal and battery (in electric models).
These workhorses come in several different classifications, including Class I, IV, and V forklifts. The 5,000 lb. capacity cushion tire forklift is what most people think of as the standard “warehouse forklift,” but they actually range dramatically in size and capability.
Common Types of Sit-Down Forklifts
Sit-down forklifts come in more varieties than I initially realized when I started in this industry. The most common types include:
- Propane (LPG) Cushion Tire Forklifts – These are your standard indoor warehouse trucks
- Electric 3-Wheel Forklifts – Great for tight spaces and indoor use
- Electric 4-Wheel Forklifts – More stable for heavier loads
- Diesel Pneumatic Tire Forklifts – Ideal for outdoor use on rough surfaces
- Specialty Models – Including swing mast forklifts for very narrow aisles
I once made the mistake of trying to use cushion tire sit-down forklifts on our outdoor yard with uneven surfaces. The trucks took a beating, and operators complained constantly. That experience taught me how important matching the right forklift to the environment really is!
FAQ: Can sit-down forklifts be used both indoors and outdoors? Yes, certain models like pneumatic tire sit-down forklifts are designed for both indoor and outdoor use. Electric cushion tire models are primarily for indoor use on smooth surfaces.
FAQ: What’s the typical lifting capacity of sit-down forklifts? Sit-down forklifts offer the widest range of lifting capacities, from 2,500 lbs to 150,000 lbs, making them suitable for various applications.
What Are Stand-Up Forklifts?
Stand-up forklifts, as you might guess, are operated from a standing position. I first encountered these when we expanded our distribution center and needed to maximize storage density with narrower aisles. The difference was immediately noticeable.
These lift trucks are also called stand-on forklifts, and they’re primarily used in warehousing applications where space is at a premium. Stand-up forklifts typically have three wheels—two for driving and one for steering—giving them a tighter turning radius than their sit-down counterparts.
Key Characteristics of Stand-Up Forklifts
Something I noticed right away about stand-up forklifts is their more compact design. They have:
- A shorter wheelbase than sit-down models
- Battery power (no internal combustion models)
- Primarily indoor application
- Lifting capacities usually between 2,000-5,500 lbs
- Controls designed for quick on/off access
The most common types of stand-up forklifts include counterbalance models and reach trucks. Reach trucks are particularly interesting because they include a pantograph mechanism that allows the forks to extend forward to retrieve loads from racking.
I remember training our team on stand-up reach trucks years ago. One operator who’d been using sit-down lifts for 20 years absolutely hated the transition at first. Three weeks later, he refused to go back to a sit-down model because the stand-up was so much more efficient for our narrow-aisle application.
FAQ: Are all stand-up forklifts electric? Yes, stand-up forklifts are exclusively battery-powered and do not come in internal combustion versions.
FAQ: What’s the difference between a stand-up counterbalance forklift and a reach truck? The main difference is that reach trucks have a scissor-like pantograph mechanism that allows the forks to extend forward into racking, while counterbalance models operate more like traditional forklifts.
Safety Comparison: Sit-Down vs. Stand-Up
Safety should always be your top priority when selecting material handling equipment. I learned this lesson the hard way when we had an incident years ago that could have been prevented with the right equipment choice.
Sit-down forklifts generally have a safety edge due to two main factors:
First, they have seat belts. This might seem obvious, but it’s hugely important. In the event of a collision or tip-over, the seat belt keeps the operator secured within the protective confines of the overhead guard and operator compartment.
Second, sit-down forklift operators are trained to stay put if the truck begins to tip over. They simply need to brace themselves, grip the steering wheel, and lean away from the direction of the fall. I’ve had operators who followed this protocol during tip-overs walk away without a scratch.
Stand-up forklifts require different safety protocols. In a tip-over situation, the operator must quickly step off the back of the forklift—requiring fast reaction time and presence of mind during a stressful situation.
Another safety consideration is the protection provided by the operator compartment. Sit-down models surround the operator on all sides, while stand-up models typically have open sides with a back guard. This affects protection in side impacts.
I once witnessed a stand-up operator narrowly avoid injury when they had to quickly step off during a beginning tip-over. Their quick reaction prevented what could have been a serious incident, but it highlighted the additional risk factor compared to sit-down models where the operator would have stayed put.
My Opinion: I believe sit-down forklifts are inherently safer for less experienced operators, while stand-up models require more skill and quick reflexes to operate safely.
FAQ: Which type of forklift has more reported accidents? Statistics don’t show a clear winner, as accident rates depend more on proper training and environment than forklift type. However, the consequences of tip-overs tend to be more severe with stand-up models.
FAQ: Do both types require the same safety training? While basic safety principles are similar, operators need specific training for each type. OSHA requires separate certification when switching between significantly different forklift types.
Ergonomics and Operator Comfort
Ergonomics might not seem like a big deal until you have operators working 8-10 hour shifts. Trust me, I’ve heard plenty of complaints when we got this aspect wrong!
The Sitting vs. Standing Debate
For operations with long travel distances, sit-down forklifts offer better operator comfort. The ability to sit reduces fatigue in the legs, knees, and lower back during extended shifts.
I recall when we switched one of our distribution centers from sit-down to stand-up forklifts without considering the travel distances. Within a week, we had multiple operators complaining about leg and back pain. We had to reconsider our approach.
For operations requiring frequent mounting and dismounting, stand-up forklifts are far superior. Operators can quickly step on and off without buckling and unbuckling seat belts each time.
Directional Changes Matter Too
Here’s something most people overlook: how often your operators change direction affects ergonomics significantly.
With sit-down forklifts, operators face forward. When traveling in reverse (which happens constantly in warehousing), they must twist their torso, neck, and shoulders to see behind them. This causes strain over time.
Stand-up operators stand sideways in the compartment. They simply need to turn their head left or right to see in either direction of travel. This reduces strain significantly during direction changes.
My Opinion: For operations where operators change direction frequently or get on and off the lift truck regularly, stand-up forklifts provide better long-term ergonomics despite the standing position.
There’s no one-size-fits-all answer here. I’ve found the best approach is to analyze your specific operational patterns and even let operators test both types.
FAQ: Which causes less operator fatigue during an 8-hour shift? For operations with long travel distances and few dismounts, sit-down forklifts cause less fatigue. For operations with frequent direction changes and dismounts, stand-up forklifts may actually cause less fatigue despite the standing position.
FAQ: Can ergonomic accessories be added to either type? Yes, both types can be improved with accessories like ergonomic seats, armrests, and cushioned mats for stand-up models.
Maneuverability and Space Efficiency
If there’s one area where stand-up forklifts truly shine, it’s maneuverability. These machines were designed specifically to work in narrower aisles and tighter spaces.
Turning Radius Comparison
Stand-up forklifts have a shorter wheelbase and, consequently, a tighter turning radius than sit-down models. This makes a huge difference when navigating narrow warehouse aisles.
I remember working on a warehouse redesign project where switching to stand-up forklifts allowed us to reduce aisle widths by nearly 2 feet. That might not sound like much, but across a 200,000 sq ft warehouse, it gave us approximately 15% more storage space—a massive return on investment!
Right Angle Stack Measurement
One specific measurement that matters is the “right angle stack”—the minimum space needed for a forklift to turn 90 degrees and enter a pallet position.
Looking at comparable 3,000 lb capacity models:
- A typical 3-wheel sit-down electric forklift: 72.1 inches right angle stack
- A typical stand-up counterbalance forklift: 68.8 inches right angle stack
That 3-inch difference allows stand-up forklifts to work in significantly tighter spaces.
Vertical Clearance Considerations
One advantage sit-down forklifts have is their lower overall height. This matters when dealing with low doorways, mezzanines, or other overhead obstructions.
I once consulted for a facility that had 7-foot doorways between warehouse sections. Their stand-up forklifts couldn’t pass through without lowering the mast completely—a major operational inconvenience. We ended up recommending low-profile sit-down models for that specific application.
My Opinion: The space savings from using stand-up forklifts in narrow-aisle applications can increase warehouse storage capacity by 10-20%, potentially eliminating the need for facility expansion.
FAQ: How much narrower can aisles be with stand-up forklifts? Typically, stand-up forklifts can operate in aisles 12-24 inches narrower than comparable sit-down models, depending on the specific models being compared.
FAQ: Do stand-up forklifts sacrifice stability for maneuverability? Not significantly. While they have a narrower wheelbase, they’re designed with appropriate counterbalancing for their rated capacities.
Control Systems and Operation
The control systems on sit-down and stand-up forklifts differ significantly, and this affects both the learning curve and operational efficiency.
Sit-Down Forklift Controls
Sit-down forklifts operate much like cars, with:
- A steering wheel
- Accelerator pedal
- Brake pedal
- Hydraulic control levers (or fingertip controls on some models)
Most new operators find these controls intuitive because they’re similar to driving a car. I’ve trained dozens of operators over the years, and most pick up the basics of sit-down operation within a few hours.
Stand-Up Forklift Controls
Stand-up forklift controls are more unique:
- A steering tiller or wheel
- A control handle that integrates travel and hydraulic functions
- No foot pedals in most models
These controls take more getting used to—they’re more like playing a video game than driving a car. The learning curve is steeper, and training time is typically longer.
I remember one experienced sit-down operator who struggled for nearly a week to get comfortable with stand-up controls. She kept trying to use her feet for acceleration and braking (which don’t exist on most stand-ups). Eventually, it clicked, and she became one of our most efficient operators.
Operating Position
Another significant difference is the operator’s position relative to the forks:
- Sit-down operators face forward, looking directly at the forks
- Stand-up operators stand perpendicular to the forks, facing sideways
This sideways positioning on stand-up forklifts makes it easier to see in both directions but takes some adjustment for operators used to facing forward.
My Opinion: While sit-down forklifts are easier to learn initially, operators who master stand-up controls often achieve greater efficiency in warehouse pick-and-put operations due to the integrated control design.
FAQ: How long does it take to train operators on each type? Most operators can learn basic sit-down operation in 1-2 days. Stand-up operation typically takes 3-5 days for proficiency, especially for operators without previous stand-up experience.
FAQ: Can operators be certified on both types with the same training? No. OSHA requires separate certification for significantly different types of powered industrial trucks. Operators need specific training for each type.
Cost Considerations
Let’s talk money! The cost difference between sit-down and stand-up forklifts can be substantial, and there are several factors to consider beyond just the purchase price.
Initial Purchase Price
For comparable 3,000 lb capacity electric models:
- Sit-down forklifts typically cost between $21,500-$25,500
- Stand-up forklifts typically cost between $26,000-$34,000
That means stand-ups can cost 20-30% more upfront. And don’t forget that battery and charger will add approximately $10,000 to either option.
I once had to justify the higher cost of stand-up forklifts to upper management for a warehouse project. The key was showing the space efficiency gains and productivity improvements that offset the higher initial investment.
Maintenance Considerations
In my experience, maintenance costs are fairly similar between the two types. However, stand-up forklifts often have fewer moving parts in their control systems, which can mean fewer maintenance issues in the long run.
Return on Investment Factors
The ROI calculation should include:
- Initial purchase price
- Operational efficiency gains
- Space utilization improvements
- Operator comfort and productivity
- Training requirements
For narrow-aisle applications, the space savings from stand-up forklifts often justify their higher cost. For outdoor operations or heavy-load applications, the versatility of sit-down forklifts usually makes more financial sense.
Bold Opinion: The higher cost of stand-up forklifts is easily justified in high-density warehousing operations where space utilization directly impacts profitability. For general-purpose or outdoor applications, the lower cost of sit-down forklifts makes them the better financial choice.
FAQ: Do stand-up forklifts have better resale value? In my experience, stand-up forklifts tend to retain their value slightly better than sit-down models, but this varies by region and market conditions.
FAQ: Are there operational cost differences between the two types? Electric models of both types have similar energy costs. The main operational cost difference comes from productivity gains or losses based on the application.
How to Choose the Right Forklift for Your Operation
After years of helping companies select the right lift trucks, I’ve developed a practical approach to making this decision. Here are the key questions you should ask:
1. What are your primary operating environments?
- Indoor only → Either type works
- Indoor and outdoor → Sit-down (especially pneumatic tire models)
- Rough or uneven surfaces → Sit-down
- Smooth warehouse floors only → Either type works
2. What are your aisle width and space constraints?
- Very narrow aisles (less than 10 feet) → Stand-up
- Standard aisles (11+ feet) → Either type works
- Low overhead clearance → Sit-down
3. What are your typical lift heights and load weights?
- Heavy loads (over 5,000 lbs) → Sit-down
- High lifting (over 20 feet) → Specific models of either type
- Standard warehouse applications → Either type works
4. What are your operators’ work patterns?
- Long travel distances → Sit-down
- Frequent on/off → Stand-up
- Frequent direction changes → Stand-up
- Full 8+ hour shifts on the forklift → Sit-down
I cannot stress enough how important it is to test the forklifts in your actual environment before making a final decision. I’ve seen too many operations make expensive mistakes by skipping this step.
Years ago, I consulted for a company that purchased an entire fleet of sit-down forklifts without proper testing. They soon discovered their aisle widths were too narrow for efficient operation. The entire fleet had to be sold at a loss and replaced with stand-up models—an expensive lesson!
Bold Opinion: The single most important factor in choosing between sit-down and stand-up forklifts is your aisle width. If space is at a premium, stand-up forklifts almost always provide the better return on investment despite their higher initial cost.
Before making a final decision, ask your dealer to arrange a demo of both types in your facility. Let your operators test them in their actual work environment and gather their feedback. They often notice practical issues that aren’t obvious on paper.
FAQ: Can a warehouse efficiently use both types of forklifts? Yes, many operations use stand-up forklifts for narrow-aisle picking and put-away while using sit-down models for receiving, shipping, and outdoor tasks.
FAQ: How often should the decision be reevaluated? Reassess your forklift selection whenever you redesign your warehouse layout, change your product mix significantly, or replace aging equipment (typically every 7-10 years).
Conclusion
Choosing between sit-down and stand-up forklifts comes down to understanding your specific operational needs. There’s no one-size-fits-all answer, despite what some forklift salespeople might tell you!
To recap the key differences:
- Sit-down forklifts excel in comfort for long travel distances, versatility for indoor/outdoor use, and higher lifting capacities
- Stand-up forklifts shine in maneuverability, space efficiency, and ergonomics for frequent direction changes and dismounting
Remember that the right choice today might not be the right choice five years from now as your operation evolves. Be willing to reassess as needed.
I encourage you to involve your operators in the decision-making process. Their comfort and efficiency directly impact your bottom line, and they often have practical insights that management might miss.
What’s your experience with these different forklift types? Have you found one to be clearly superior for your operation? Share your thoughts and experiences in the comments below!
Safety should always be your top priority, regardless of which type you choose. Ensure all operators receive proper training specific to the forklift type they’ll be operating, and remember that OSHA requires separate certification for different types of powered industrial trucks.
Take the time to make the right choice—your warehouse efficiency, operator satisfaction, and bottom line will thank you!